8 Benefits of Crane Modernization
Increased production requirements may demand more capacity, faster operating speeds, better controls, or automation capabilities. Reliability may have deteriorated, causing unscheduled shutdowns and increased production costs. Parts may be obsolete, resulting in high spare parts costs and long lead times. Inspections may show excessive wear or non-compliance with current safety standards or practices.
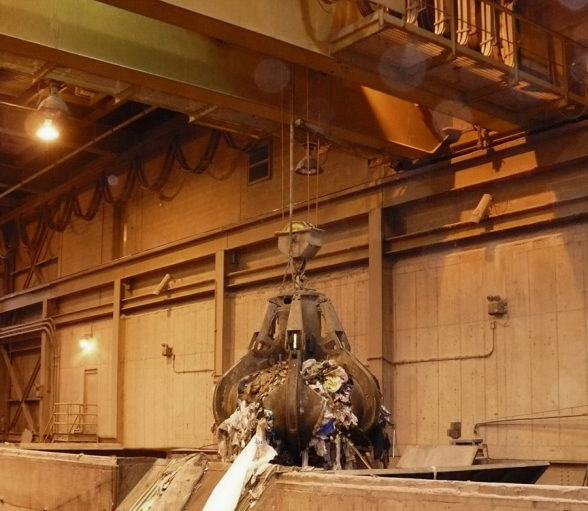
Waste-to-Energy Bridge Crane Automation
Updated bridge cranes with semi-automated controls increased speed, reliability, and productivity, nearly doubling throughput from 200 to 400 tons of processed waste per day. All-new Magnetek-brand IMPULSE•VG+ and G+ Variable Frequency Drives and hoist motors were installed, as well as PLC interfaces to ensure continuous operation and maximum performance. View Case Study.
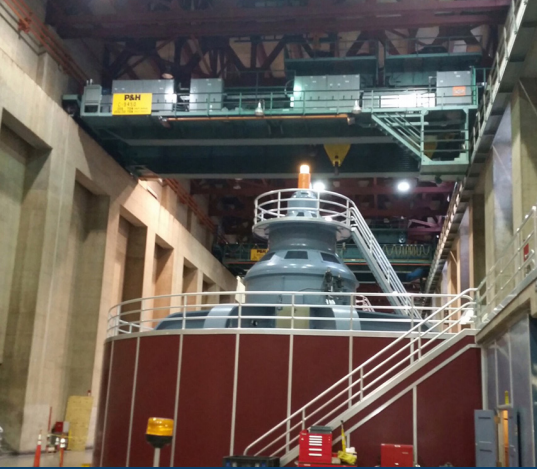
Hoover Dam Crane Control Modernization
The Hoover Dam Power Plant houses four 300-ton cranes that are used to move and maintain the 17 main vertical hydraulic turbines. Improving productivity, safety, and reliability, we supplied Magnetek-brand IMPULSE•VG+ and G+ Variable Frequency Drives and XLTX radio remote controls on each of the cranes. We also provided crane-to-crane communication for PLC assisted synchronized motion control on hoists, trolleys, and bridges. View Case Study.
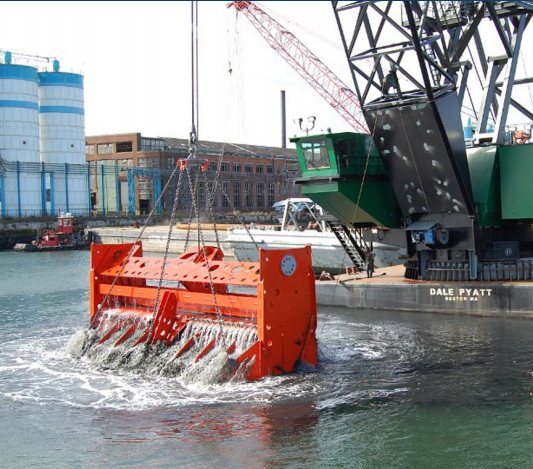
Dredge Crane Project
Magnetek-brand IMPULSE•VG+ and G+ Variable Frequency Drives with Bucket Control Custom Software were paired with Blue Max® Motors to control the highest-producing dredge crane operating in North America. With the new system, the crane’s service life was extended from 20,000 hours to more from 20,000 hours to more than 200,000 hours. View Case Study.